FS350M
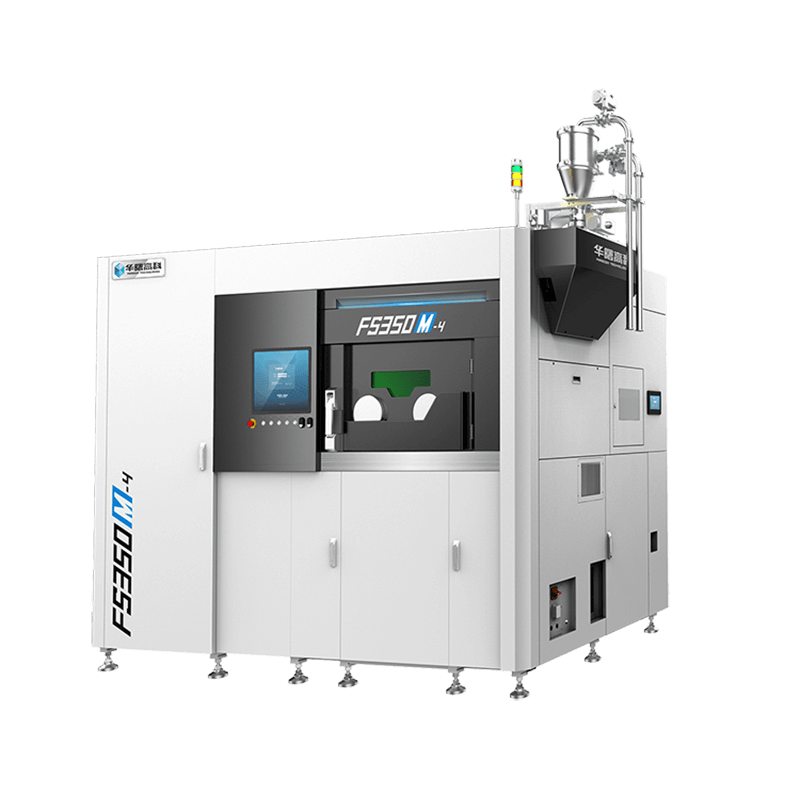
Features/ Selling points
HIGHLY PRODUCTIVE
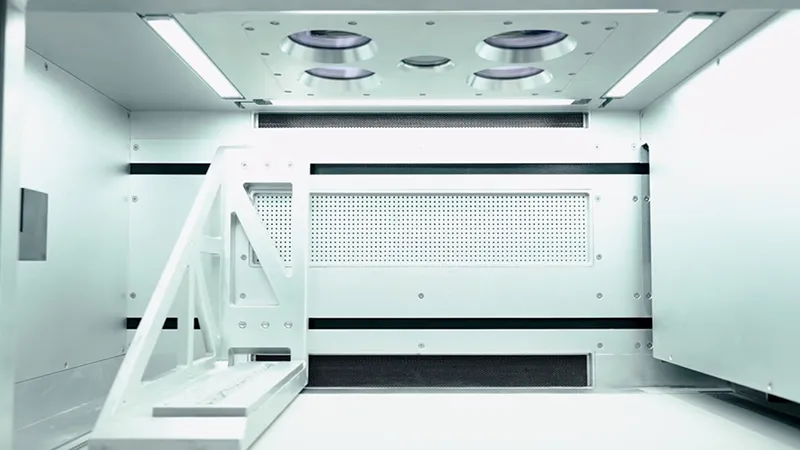
Featuring an expanded build cylinder of 433 × 358 × 400 mm, the FS350M is capable of producing large metal parts from a wide range of powder materials. With multi-laser configuration and thicker layer process, the FS350M offers optional Beam Shaping Technology, greatly enhancing the production efficiency.
SAFE & EFFICIENT

Equipped with advanced multi-laser scanning strategy and calibration algorithms, the FS350M offers optimal build efficiency, and uniformed part performance in overlapping areas. The closed-loop Powder Management System, intelligent recoating control, and advanced layered gas flow design allow for efficient, yet uniformed melting process of metal powder.
COST-EFFECTIVE
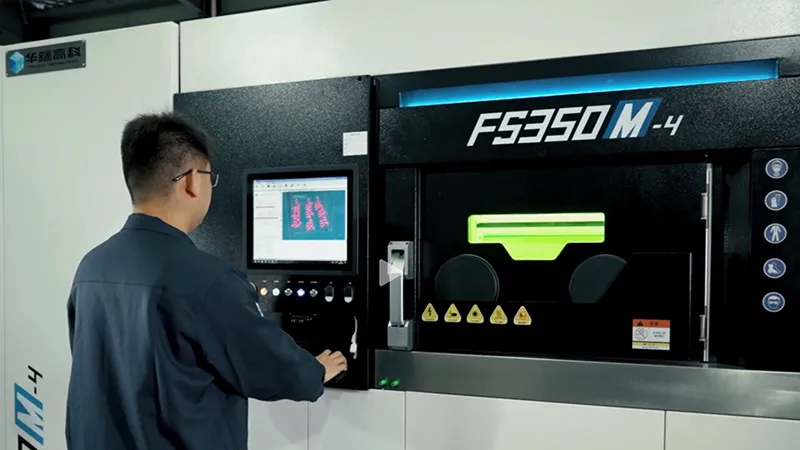
The FS350M features a machine footprint as small as 6.03 M3 with an integrated three-stage Filtration System. In an additive factory setting, FS350M enables high density layout to achieve maximum throughput per floor area at economical additive manufacturing cost. The FS350M is a truly open platform which offers the user a high degree of control to tailor processing parameters for industrial application requirements and costcompetitive metal additive manufacturing.
Technical Data
External Dimensions (L × W × H) | 3260 × 1850 × 2300 mm |
Build Cylinder Size (L × W × H) | 433 × 358 × 400 mm (Incl. build plate) |
Net Weight | Approx. 3300 kg |
Layer Thickness | 0.02 ~ 0.1 mm |
Maximum Scan Speed | 10 m/s |
Laser Type | Fiber laser, 6 × 500 W |
Scanner | F theta lenses |
Inert Gas Protection | Argon/ Nitrogen |
Average Inert Gas Consumption in Process | 3-5 L/min |
Operating System | 64 bit Windows 10 |
Comprehensive Software | BuildStar, MakeStar |
Key Software Features | Open machine key parameters, real-time build parameter modification, three-dimensional visualization, diagnostic functions |
Data File Format | STL |
Power Supply | 400 V±10%, 3~/ N/ PE, 50 Hz, 50 A |
Operating Ambient Temperature | 22-28℃ |
Materials | 316L, Ti6Al4V, AlSi10Mg, ST-1, Maraging Steel Grade 300, etc. |
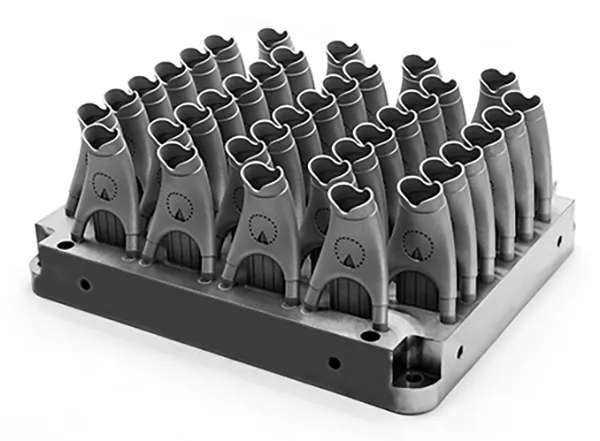
Titanium Bicycle Seat Stay Yokes
Machine: FS350M-4
Material: Ti6Al4V
Size: 433 x 358 x 116 (H) mm (38pcs in one build)
Layer thickness: 0.06 mm
Build Time: 24 Hours
Batch production of titanium bicycle seat stay yokes using the FS350M-4 demonstrates a leap in efficiency and innovation. In just 24 hours, 38 components are 3D printed, achieving a 60% increase in efficiency compared to traditional casting methods. The flat aero tube design of these yokes not only streamlines production but also enhances cycling comfort by reducing the impact of the wheelset on the frame. This advanced manufacturing approach not only speeds up production but also contributes to a smoother, more comfortable ride.