FLIGHT 403P
Impressive Detail Resolution.
The FLIGHT® Technology unlocks the next level of laser powder bed fusion productivity for industrial-quality parts offering extremely fine details. Also, thanks to the advanced laser powder bed fusion technology, additive agents and other consumables are not required; therefore, enabling lower operational cost and sustainable manufacturing.
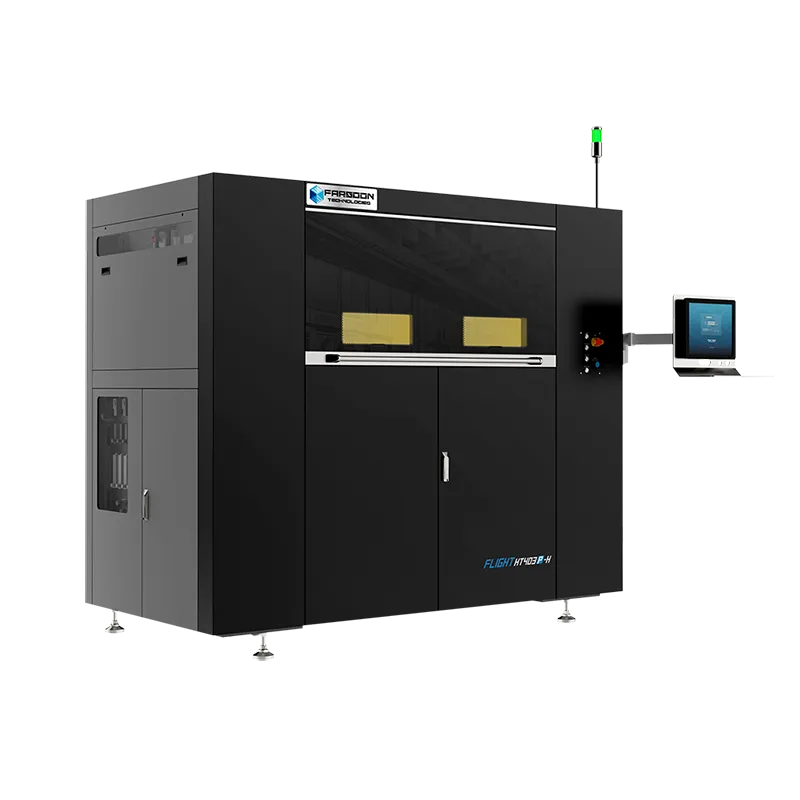
Features/ Selling points:
FIBER LASER

FLIGHT® Technology or FIBER LIGHT® Technology takes advantage of powerful fiber lasers in place of the standard CO2 lasers found in standard laser sintering systems. A fiber system is capable of delivering greatly increased power to the powder bed. Due to the more robust and stable nature of a fiber laser system as compared to a CO2 system FLIGHT® Technology also provides increased laser longevity which is key when considering ROI for manufacturing applications.
FAST PRODUCTION SPEED
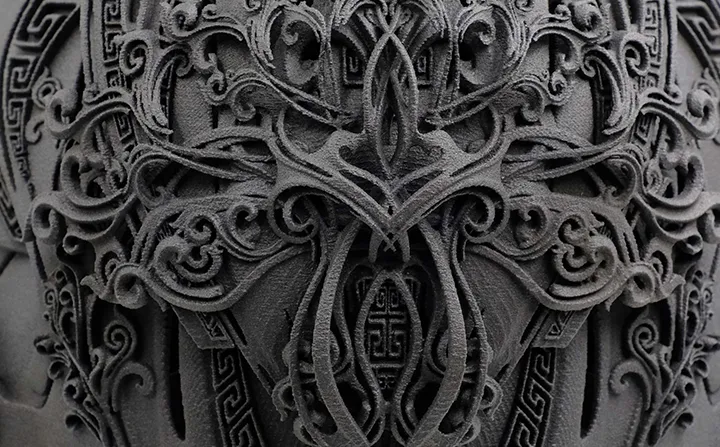
With robust laser power, improved energy distribution to the material, and smaller laser spot size, the new FLIGHT® Technology achieves significantly higher power density upon reaching the surface of the powder bed, thus enabling the full sintering of powder in an extremely short amount of time. With scanning speed of over 20m/s (66 ft/s), FLIGHT® Technology is able to achieve extreme sintering speeds that pushes the additive manufacturing productivity to a new level.
GOOD PRINTING QUALITY
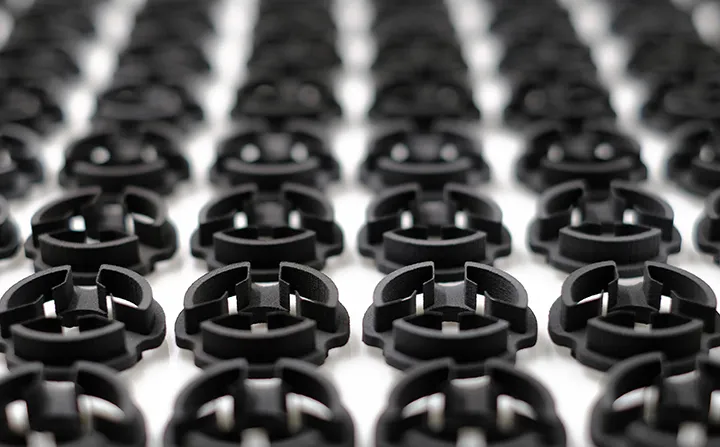
FLIGHT® Technology is able to achieve a more homogenous energy distribution over the processing surface, and a finer spot size compared to the standard laser sintering systems, while at the same time ensuring good energy penetration throughout the entire process. This results in improved feature detail compared to other plastic powder-based technologies with feature details as small as 0.3mm (0.012 inch) while still achieving the part property benefits of standard laser sintering.
Technical Data
External Dimensions (L×W×H): | 2540×1320×2220 mm |
Build Cylinder Size (L×W×H): | 400×400×540 mm (HT403P) |
Net Weight: Approx. | 3100 kg |
Layer Thickness: | 0.06~0.3 mm |
Maximum Scan Speed: | 20 m/s |
Laser Type: | Fiber Laser, 2×300W |
Scanner: | High-precision galvo system |
Maximum Chamber Temperature: | 220℃ |
Temperature: | Continuous real-time surface temperature monitoring |
Operating System: | 64 bit Windows 10 |
Comprehensive Software: | BuildStar, MakeStar |
Key Software Features: | Open machine key parameters, real-time build parameter modification, three-dimensional visualization, diagnostic functions |
Data File Format: | STL |
Power Supply: | 380 V ± 10%, 3~/N/PE, 50 Hz, 32 A |
Operating Ambient Temperature: | 22-28℃ |
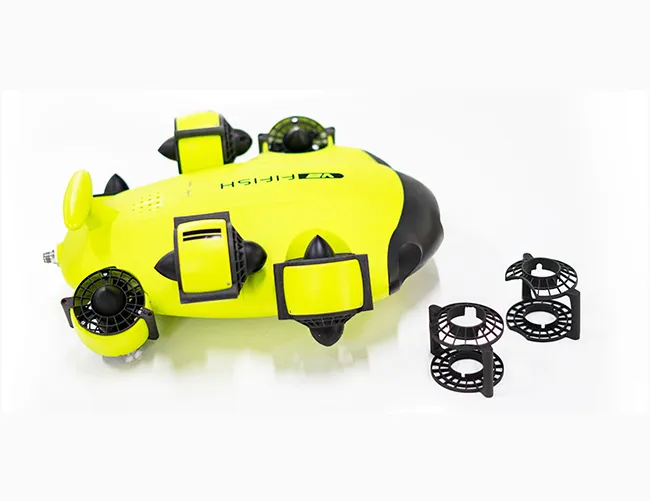
Underwater ROV Propelled by FLIGHT® Technology
Machine: FLIGHT® HT403P
Material: FS3300PA-F (PA12 with carbon black)
Build Time: 150 thruster protective covers produced in one day
QYSEA Technology, a leading Underwater Remote Operated Vehicles (ROV) manufacturer, introduced one of the most popular consumers ROV-Fifish V6 with robust performance. Since 2018, QYSEA Technology adopted Farsoon’s latest FLIGHT® Technology for their development process and series production needs. During the year of 2019 QYSEA has successfully fabricated more than 30,000 thruster protective covers on FLIGHT® HT403P systems for end-use parts in their consumer ROV production.