FLIGHT HT601P-4
Large-format Polymer LPBF system designed for high-speed, industrial serial production.
The FLIGHT® HT601P is a high-speed polymer LPBF system with four 300W fiber lasers, enabling 20 m/s scanning-faster than traditional CO2 lasers. Its 600 × 600 × 600 mm build volume supports industrial-scale production. Operating at up to 220℃, it processes high-performance materials like PA6 and TPU. With advanced powder handling and multi-laser strategies, it outperforms competitors in speed, efficiency, and part quality.
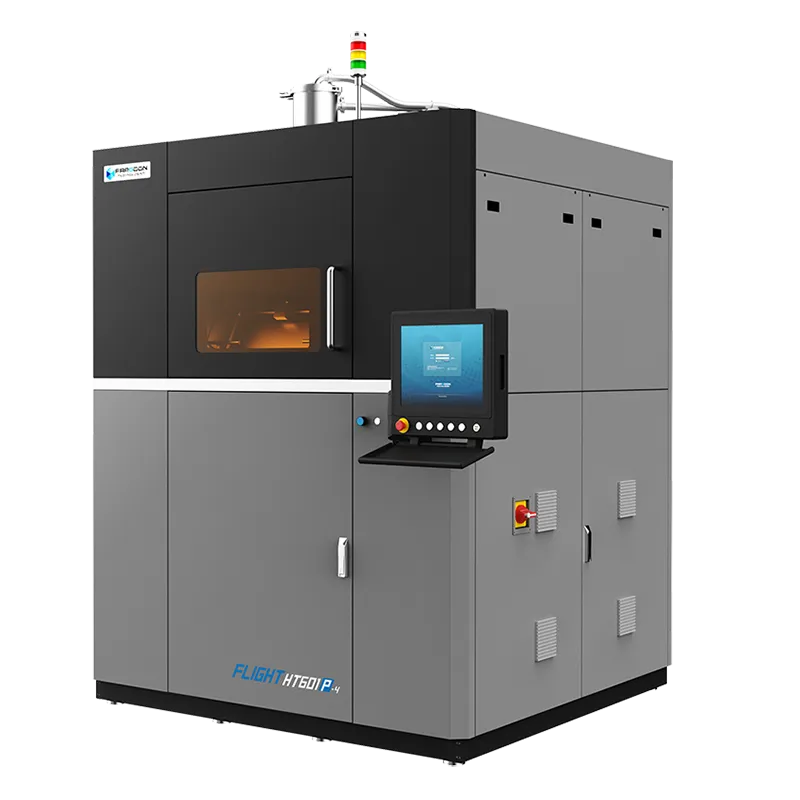
Features/ Selling points:
QUALITY + RELIABILITY
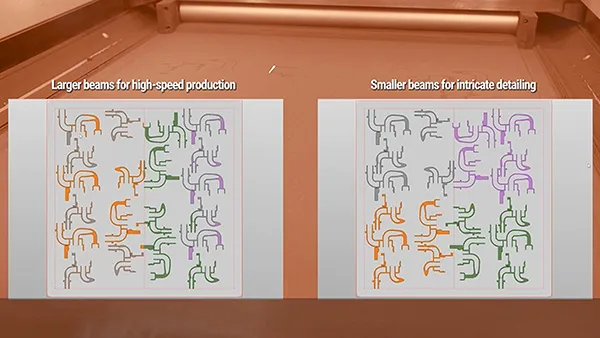
The Flight® HT601P-4 ensures reliable production with advanced quality assurance features. Its innovative powder supply method enables efficient, uniform recoating, while an advanced control card ensures stable laser power. Multi-laser scanning modes optimize productivity or certification compliance, and an optical cooling system maintains consistency in part properties and surface quality.
MATERIAL CAPABILITY
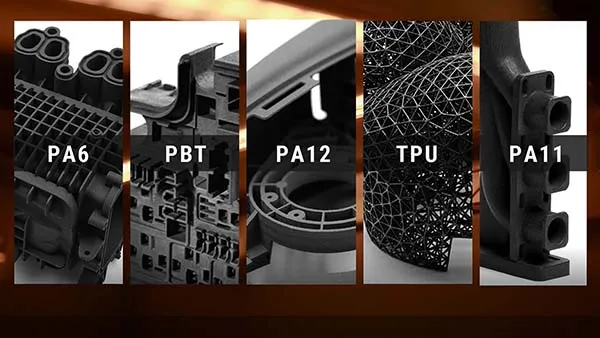
The Flight® HT601P-4 supports high-performance materials like PA6, PBT, PA11, PA12, and TPU with chamber temperatures up to 220°C. Its multi-zone temperature control and infrared thermal monitoring ensure uniform heat distribution. An open parameter strategy allows users to customize processing, enabling innovation in aerospace, automotive, and medical industries.
FACTORY INTEGRATION
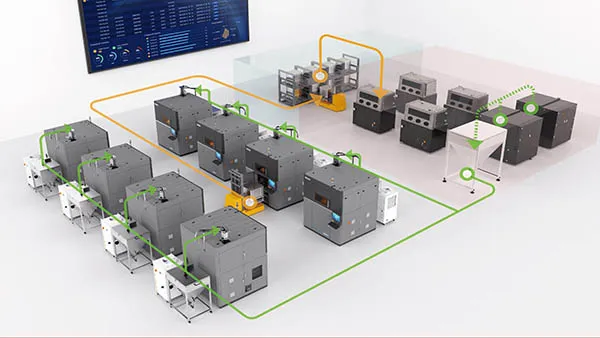
The Flight® HT601P-4 ensures seamless large-scale production with advanced automation. Its Powder Management System (PMS) enables efficient recycling, mixing, and sieving across multiple machines. Smart production line integration centralizes powder handling, build transfer, cooling, and breakout, optimizing workflow for high-efficiency, automated manufacturing with minimal manual intervention.
Technical Data
External Dimensions (L×W×H): | 1862 × 1832 × 2350 mm |
Build Cylinder Size (L×W×H): | 600 × 600 × 600 mm |
Net Weight: Approx. | 3300 kg |
Layer Thickness: | 0.06~0.3 mm |
Maximum Scan Speed: | 20 m/s |
Laser Type: | Fiber Laser, 4 ×300W |
Scanner: | High-precision three-axis galvo system |
Maximum Chamber Temperature: | 220℃ |
Temperature: | Continuous real-time surface temperature monitoring |
Operating System: | 64 bit Windows 10 |
Comprehensive Software: | BuildStar, MakeStar |
Key Software Features: | Open machine key parameters, real-time build parameter modification, three-dimensional visualization, diagnostic functions |
Data File Format: | STL |
Power Supply: | 380 V ± 10%, 3~/N/PE, 50 Hz/ 60 Hz, 50 A |
Operating Ambient Temperature: | 22-28℃ |
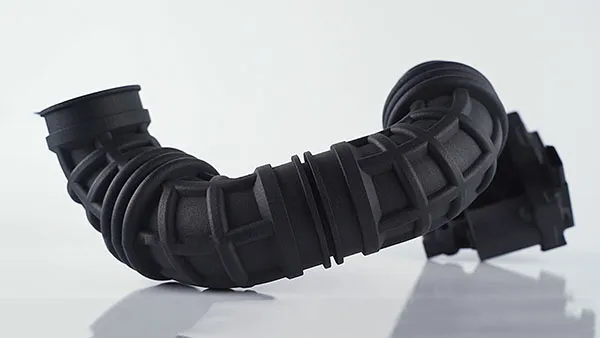
Automotive Connector Pipes
Machine: Flight® HT601P-4 Quad-laser system
Material: FS6130CF-F (Carbon Fiber reinforced PA6 with carbon black)
The 3D-printed automotive connector pipes, produced on the Flight® HT601P-4 quad-laser system, utilize FS6130CF-F, a carbon fiber-reinforced PA6 with carbon black. This high-strength, heat-resistant material ensures durability and precision. The lightweight yet robust pipes enhance performance in automotive fluid and air management systems, offering superior mechanical properties and design flexibility.