FS811M
Metal 3D Printing Platform
Large-format Metal Laser Sintering System
boasts high productivity
In response to escalating demands for enhanced manufacturing efficacy, dependability, and expanded build capacities across aerospace, oil & gas, energy, and automotive sectors, we engineered the FS811M. This advanced system is meticulously optimized for high-volume production of bespoke applications, delivering superior quality outputs and facilitating seamless operational workflows.
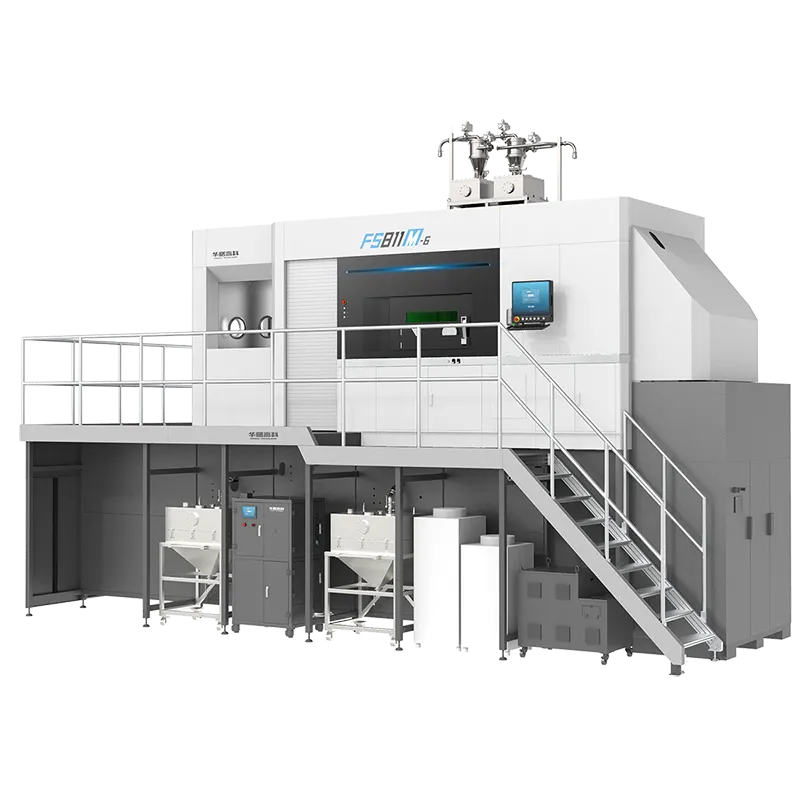
Features
EXTRA-LARGE BUILD VOLUME
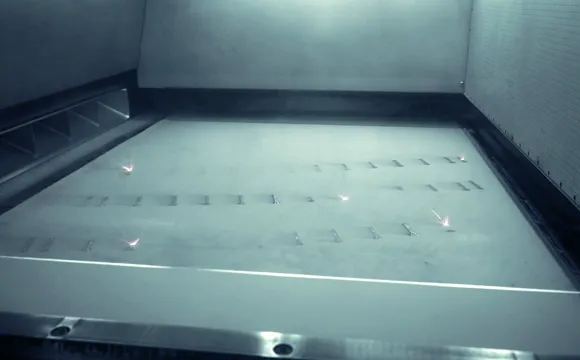
With a build platform size of 840 × 840 × 960mm and build volume of 677 Liters, the FS811M features one of the largest build volumes in metal laser powder bed fusion market. Equipped with up to 12 robust fiber lasers, the high-speed galvo system boosts high production yield up to 300cm3/h.
QUALITY & RELIABILITY
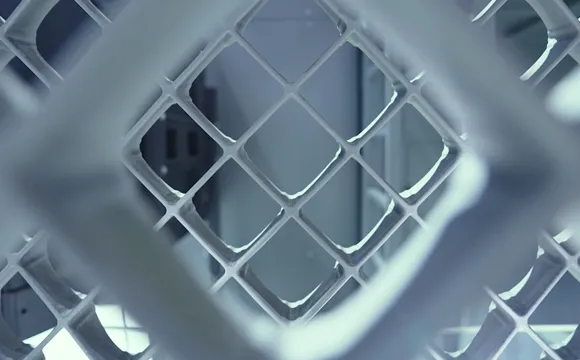
The FS811M multi-layer gas flow with advanced wind-wall design ensures real-time particle removal throughout the whole oversized chamber. The excellent air tightness design of FS811M build chamber enables extreme oxygen content, and low inert gas consumption, ensuring the part quality consistency while reducing operational costs. The powerful permanent filtration system allows uninterrupted, reliable process for extreme build times.
OPERATION EASE
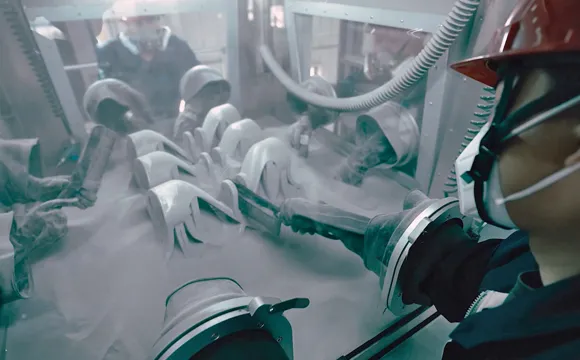
The FS811M build chamber is equipped with both front and rear doors for ease of operation and maintenance. Once the build is completed, the part cylinder can be transferred to powder breakout station and part extract station via an integrated conveyor system. The breakout station is fully enclosed and can be accessed through glove boxes on all 4 sides, allowing operators for powder removal and detail cleaning under safe inert atmosphere.
Technical Data
External Dimensions (L × W × H): | 8500 × 4500 × 4970 mm |
Build Cylinder Size (L × W × H): | 840 × 840 × 960 mm (Incl. build plate) |
Net Weight: Approx. | 25000 kg |
Layer Thickness: | 0.02 ~ 0.1 mm |
Maximum Scan Speed: | 10 m/s |
Laser Type: | Fiber laser, 6 × 500 W or 8 × 500 W or 10 × 500 W or 12 × 500 W |
Scanner: | F theta lenses |
Inert Gas Protection: | Argon/ Nitrogen |
Average Inert Gas Consumption in Process: | 12-15 L/min |
Operating System: | 64 bit Windows 10 |
Comprehensive Software: | BuildStar, MakeStar |
Key Software Features: | Open machine key parameters, real-time build parameter modification, three-dimensional visualization, diagnostic functions |
Data File Format: | STL |
Power Supply: | 400 V ± 10%, 3~/ N/ PE, 50 Hz, 80 A |
Operating Ambient Temperature: | 22-28℃ |
Materials: | IN625, IN718, TA15, Ti6Al4V, etc. |
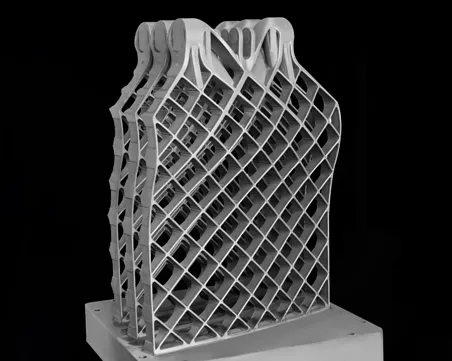
Stabilizer Fin of Rocket
Machine: FS811M-U-6
Material: TA15
Size: 750 x 195 x 1035 (H) mm
Meticulously crafted with precision using our cutting-edge FS811M metal 3D printing technology verses traditional manufacturing methods, the production of the stabilizer fin showcases numerous benefits, including simplified processes, superior quality, and the freedom to create innovative designs that were once deemed impossible. Intricate geometries can be produced with unmatched precision, resulting in parts that are lighter, stronger, and more efficient than ever before.